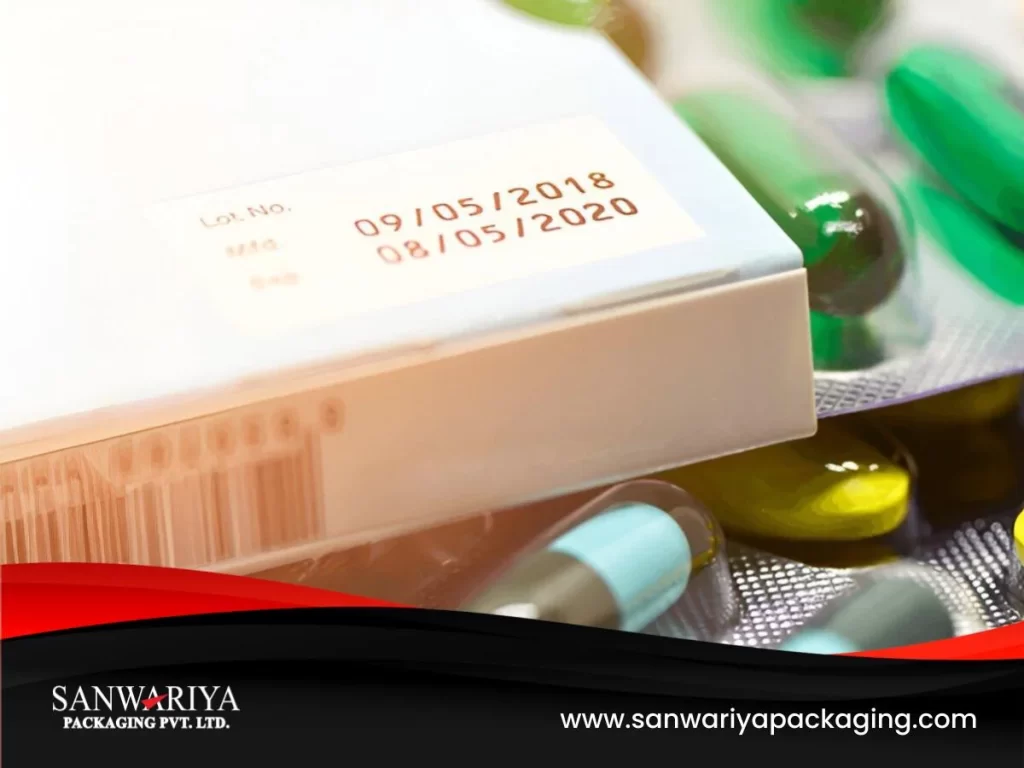
Pharmaceutical packaging is far more than a protective shell—it is an essential component of drug safety, regulatory compliance, and patient experience. Every step, from selecting raw materials to ensuring safe disposal, plays a critical role in maintaining drug efficacy, preventing counterfeiting, and meeting global regulatory standards.
With increasing counterfeit threats, evolving compliance regulations, and growing sustainability concerns, the pharmaceutical industry must continuously innovate its packaging strategies. This blog explores the entire lifecycle of pharmaceutical packaging and what it takes to ensure medicines reach consumers safely and securely.
Material Selection: The Foundation of Safe Packaging
Selecting the right materials is the first step in ensuring the safety, stability, and compliance of pharmaceutical packaging.
Key Considerations:
- Regulatory Compliance – Packaging materials must meet standards from regulatory bodies like FDA, EMA, WHO, and TGA to avoid product recalls and market rejections.
- Product Protection – Packaging must shield drugs from moisture, oxygen, light, and contamination, preserving efficacy.
- Sustainability – Eco-friendly packaging, such as PVC-free blister packs and recyclable aluminum foils, is becoming a priority worldwide.
Example: Leading pharma companies are transitioning to biodegradable blister packs to minimize environmental impact while maintaining drug integrity.
Packaging Design: Security, Compliance & User Experience
A well-designed pharma package must balance security, ease of use, and regulatory adherence.
Essential Design Elements:
- Anti-Counterfeit & Tamper-Proof Features – Technologies like holograms, QR codes, and RFID tracking authenticate genuine products.
- Clear & Compliant Labeling – Labels must include dosage, batch numbers, expiry dates, and country-specific regulatory markings.
- User-Friendly Features – Child-resistant closures prevent accidents, while easy-to-open packaging supports elderly patients.
Example: Under the European Falsified Medicines Directive (FMD), pharmaceutical companies must implement serialization to track every drug unit from production to patient use.
Manufacturing & Printing: Precision, Security & Quality Control
Once the design is finalized, packaging moves to high-precision manufacturing to ensure accuracy and compliance.
Key Manufacturing Steps:
- Advanced Printing Technology – High-resolution batch numbers, barcodes, and authentication features are integrated.
- Stringent Quality Control – Every package undergoes defect inspections, material integrity checks, and compliance validation.
- Market-Specific Customization – Packaging is tailored with region-specific labels and multilingual instructions.
Example: The U.S. Drug Supply Chain Security Act (DSCSA) mandates that all pharmaceutical packages include a unique identifier to ensure supply chain transparency.
Filling & Sealing: Ensuring Drug Integrity
This stage involves encasing the pharmaceutical product securely to prevent contamination and maintain potency.
Critical Steps:
- Primary Packaging – Includes blister packs, vials, ampoules, and sachets, designed to protect the drug.
- Sealing & Integrity Testing – Techniques like heat sealing, vacuum sealing, and leak testing prevent contamination.
- Serialization & Traceability – Every package receives a unique tracking code to combat counterfeiting.
Example: Leading pharma brands now embed RFID tags in packaging to track medicine movement from factory to pharmacy.
Distribution & Storage: Protecting Medicines in Transit
Once packaged, medicines require careful handling, storage, and distribution to retain quality.
Key Considerations:
- Cold Chain Logistics – Vaccines and biologics need temperature-controlled packaging to prevent degradation.
- Shock & Impact Resistance – Packaging must withstand transport stress, humidity, and temperature fluctuations.
- Global Compliance – Different countries have unique labeling, storage, and distribution regulations.
Example: COVID-19 vaccines required ultra-cold storage packaging at -70°C to maintain potency during transport.
The Future of Pharmaceutical Packaging
The industry is evolving rapidly with cutting-edge innovations aimed at enhancing security, sustainability, and patient convenience.
Emerging Trends:
- Smart Packaging – Uses temperature sensors and tamper-detection to ensure product integrity.
- Blockchain & AI for Supply Chain Transparency – Strengthens anti-counterfeit efforts by tracking each unit through blockchain.
- 100% Recyclable & Biodegradable Packaging – Meets global sustainability regulations and consumer demand.
Prediction: By 2030, over 70% of pharmaceutical companies will transition to smart and eco-friendly packaging to align with global sustainability goals.
Beyond Protection: Packaging That Builds Trust
Pharmaceutical packaging does more than safeguard products—it underpins drug safety, regulatory integrity, and patient confidence. From material selection to final delivery, every step in the packaging lifecycle is critical to ensuring that medicines arrive in their purest, most effective form.
At Sanwariya Packaging, we go beyond the basics. We specialize in delivering secure, innovative, and globally compliant packaging solutions that not only meet but exceed industry expectations. Our advanced anti-counterfeit foils, precision multicolor printing, and sustainable materials help protect your brand and your consumers.
As the industry embraces smart technologies and eco-friendly breakthroughs, we’re leading the charge—empowering pharmaceutical companies to stay compliant, competitive, and future-ready in a rapidly evolving landscape.
Is Your Packaging Future-Ready?
Looking for secure, compliant, and innovative pharmaceutical packaging solutions? Contact us today to explore how our cutting-edge packaging technologies can enhance your pharmaceutical products.