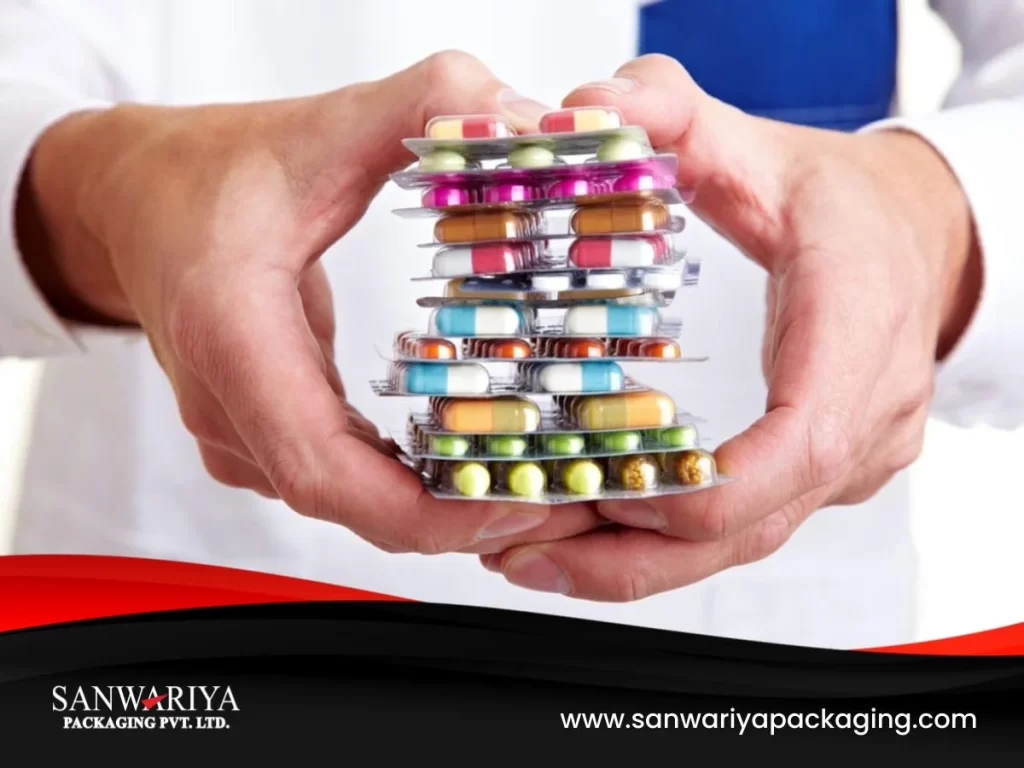
Counterfeit Drugs Are a Global Threat
Counterfeit medications represent one of the most significant public health threats globally.
According to the World Health Organization (WHO), approximately 1 in 10 medical products in developing countries is either fake or substandard. This alarming statistic presents major challenges for pharmaceutical companies, including patient safety, brand integrity, and legal liabilities. The need to combat this issue has never been more critical. Advanced security foils are now leading the charge in anti-counterfeit protection.
Technologies like QR codes, microtext, UV-sensitive inks, and nano-imprinting are revolutionizing how pharmaceutical companies safeguard their packaging — and their reputation.
In this blog, we’ll explore:
- How these foils offer multi-layered protection
- How they integrate into existing packaging lines
- What’s next in the future of anti-counterfeit solutions
The Counterfeit Challenge in Pharma Supply Chains
Pharma supply chains are vast and vulnerable. With products moving through multiple hands — from manufacturers to distributors and retailers — counterfeiters exploit weak points in packaging systems.
Key challenges include:
- Low traceability in global distribution
- Tampering during transit
- Inadequate recall tracking
These threats demand smarter, tamper-evident, and verifiable packaging.
Want a foundational overview? Read: Why Security Foils Are Critical in Preventing Counterfeit Medicines
How Advanced Security Foils Work to Prevent Counterfeiting
Security foils today are engineered with both visible and covert features. These include:
- Microtext Printing: Legible only under magnification, making duplication nearly impossible.
- Multi-Layer Foils: Built to reveal tampering with delamination or color-shifting effects.
- Serialized QR Codes: Each unit has a unique, traceable digital identity.
- UV-Sensitive Inks: Only visible under ultraviolet light — invisible to counterfeiters.
These features combine to offer layered, intelligent defense — a must-have in modern pharma packaging.
Why Compliance and Brand Teams Must Prioritize Secure Foils
Today’s packaging does more than protect—it communicates trust. Security foils address multiple needs:
- Regulatory Compliance: Meet DSCSA, EU FMD, and Latin American mandates with serialization-ready solutions.
- Strengthen Consumer Trust: Allow patients and pharmacists to instantly verify authenticity via QR or holograms.
- Legal Protection: Reduce liability and costly recalls by ensuring product traceability.
- Supply Chain Visibility: Track every unit with blockchain or cloud-based solutions for real-time auditing.
Innovations Powering Security Foils
Sanwariya’s advanced foil solutions integrate next-gen technology, including:
- Nano-Imprinting: Creates effects visible only at specific angles — unforgeable and elegant.
- Digital Watermarks: Covert codes read via mobile apps for fast, secure verification.
- Reverse-Side Printing: Hidden data embedded under the foil layer—an extra line of defense.
Together, these innovations transform packaging into a smart security system.
Future Trends in Anti-Counterfeit Packaging
Tomorrow’s pharma packaging will be smarter and even more connected:
- Blockchain-Linked Packaging: Track the journey from factory to pharmacy.
- AI Authentication: Instant counterfeit detection through mobile scanning and machine learning.
- Biometric Integration: Linking packaging to patient IDs for personalized verification.
Forward-thinking companies are already testing these tools — and gaining a competitive edge.
In an era of digital threats and global distribution, anti-counterfeit packaging is not optional — it’s mission-critical. Advanced security foils give you the tools to stay ahead, meet global compliance, and earn consumer trust.
At Sanwariya Packaging, we offer cutting-edge foil solutions tailored for pharma companies. From tamper-evident designs to blockchain-compatible serialization, we make your packaging safer, smarter, and future-ready.
📩 Let’s secure your packaging together.
Contact Sanwariya Packaging to build a tamper-proof tomorrow.